Tata Motors is making a significant impact on the commercial vehicle sector with the launch of its advanced spare parts warehouse in Guwahati. This state-of-the-art facility is designed to enhance customer service and operational efficiency across the North East region. In an exclusive interview with N. Balasubramanian and Raghul Sivaguru, Vikram Agarwal, Head of Spares and Non-Vehicular Business at Tata Motors Commercial Vehicles, delves into the innovative features and strategic importance of this new warehouse.
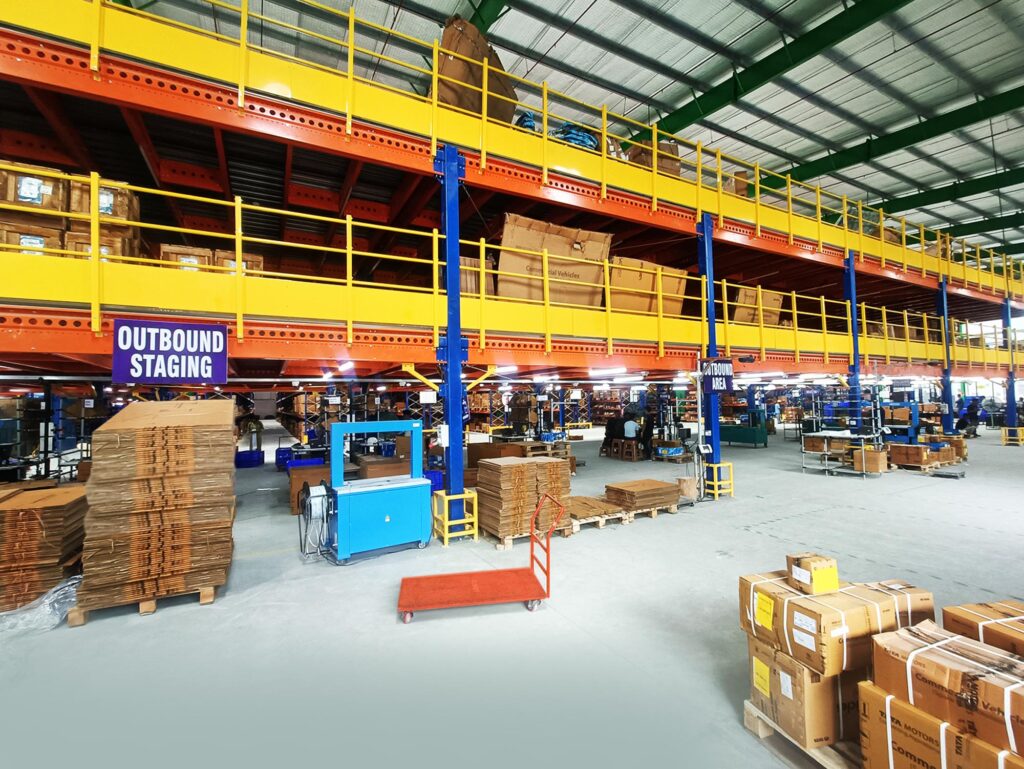
What is the motive behind Tata Motors’ new Spare Parts Warehouse in the northeastern region of India? What are the facilities integrated into this warehouse?
Tata Motors has taken a significant stride in enhancing customer service and operational efficiency with the unveiling of its state-of-the-art spare parts warehouse. Strategically located in Guwahati to cater to the growing demand for commercial vehicles in the northeastern region, this cutting-edge facility is poised for quick delivery of parts for Tata Motors’ channel partners and customers. The warehouse boasts an advanced digitized infrastructure seamlessly integrated with Tata Motors’ Authorized Service Stations, enabling faster turnaround time for repairs and maintenance. This digital integration empowers Tata authorized service stations to consistently meet and exceed customer expectations.
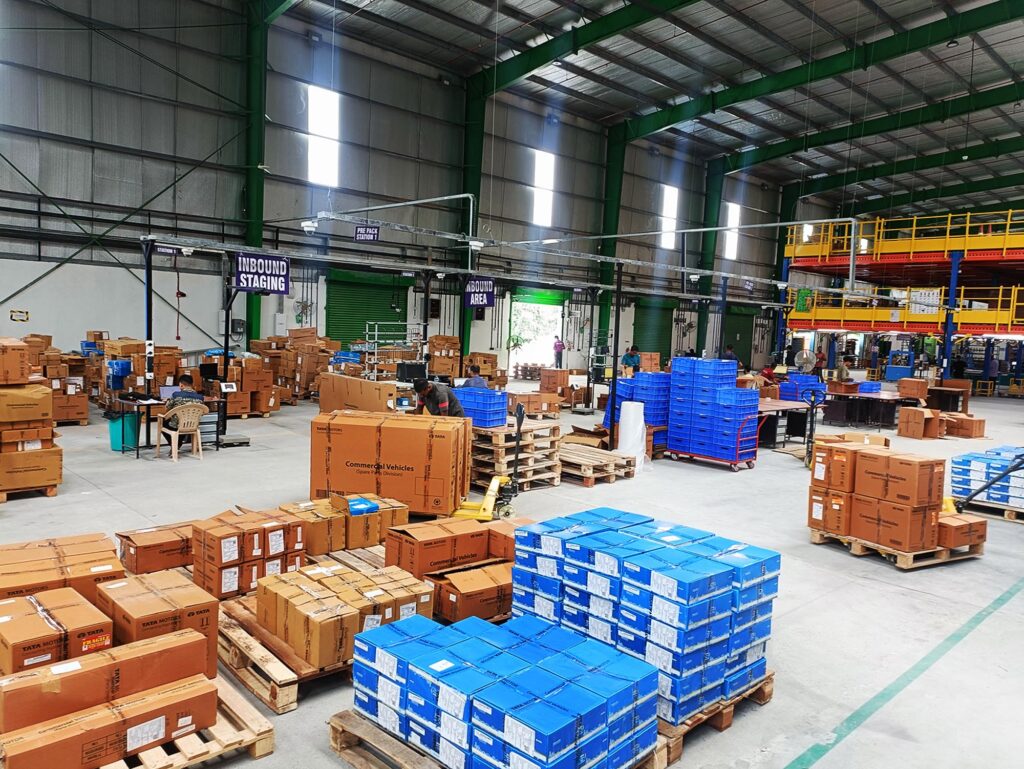
Additionally, the warehouse is integrated with a Transportation Management System (TMS) for efficient route planning and an Advanced Warehouse Management System (AWMS) for managing spare parts inventory without manual intervention. Designed for maximum space utilization, the Guwahati-based warehouse has dedicated storage areas for cowl, cab, and chassis frames that are managed by advanced material handling equipment for fast and safe operations. The world-class infrastructure and stringent safety measures facilitate efficient internal movement of spare parts. Cutting-edge storage systems, such as gravity spiral and vertical reciprocating conveyors, enhance operational productivity. The facility is designed to be energy efficient with smart materials that optimize the use of natural light.
These state-of-the-art systems streamline the distribution process while mitigating potential errors, ensuring the highest standards of quality and reliability. By ensuring quicker delivery of spare parts across the northeastern region, Tata Motors has addressed a crucial aspect of delivering high vehicle uptime – a key determinant of overall operational efficiency for customers. With readily available spare parts, vehicle downtime is minimized, enabling businesses to operate optimally and maintain seamless logistics operations. By fostering a more efficient and streamlined logistics chain, Tata Motors is not only enhancing its operational capabilities but also contributing to the region’s economic growth and development.
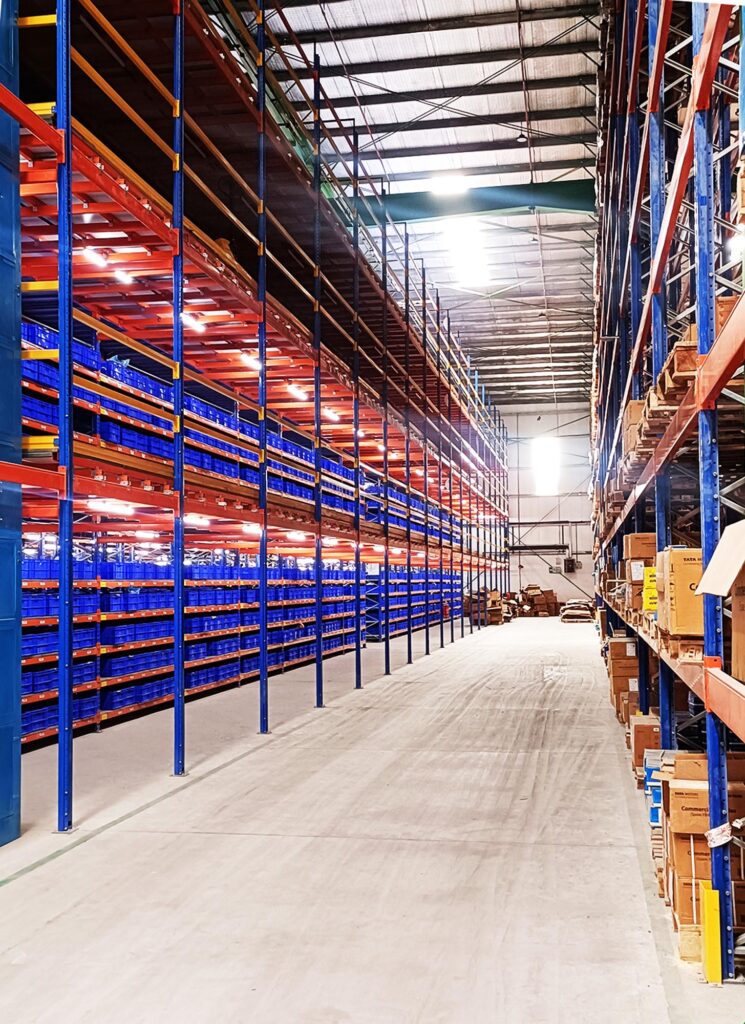
What is the driving force behind choosing Delhivery as the Logistics Service Provider? What were the amenities promised from their end, exclusively at the transit of CV spare parts? Is this warehouse able to deliver spares to the customers of the 2,500+ touchpoints of Tata Motors across India, or is it to cater to a specific region?
To enhance customer satisfaction in the northeast region, Tata Motors has partnered with Delhivery, one of India’s leading integrated logistics providers. This strategic alliance leverages Delhivery’s extensive network and cutting-edge technology in warehousing and transportation. By leveraging these advanced logistics solutions, Tata Motors aims to significantly reduce the turnaround time from order placement to delivery, thereby meeting and exceeding customer expectations in this crucial market.
Tata Motors has strategically set up six cutting-edge warehouses across the country to service the requirements of various regions efficiently. The company has invested in a warehouse in Guwahati to cater specifically to customers in the northeastern states of India, ensuring timely deliveries and enhanced customer satisfaction in this region.
What are the potential challenges in deciding what to store and how much to store at the warehouse? What role do Big Data and AI play in this regard? Also, are there any specific measures taken to store metal parts & rubber parts, which are reactive to atmospheric conditions?
Spare parts consumption is a dynamic process that depends on factors like vehicle usage and seasonal changes. To address this, Tata Motors has implemented an advanced, automated parts replenishment system. This intelligent system adapts to evolving consumption patterns, ensuring warehouses are always optimally stocked. Taking this a step further, we are progressively increasing the use of AI and ML capabilities to enhance the predictive models. These innovations promise to elevate customer experience through faster and more accurate parts availability.
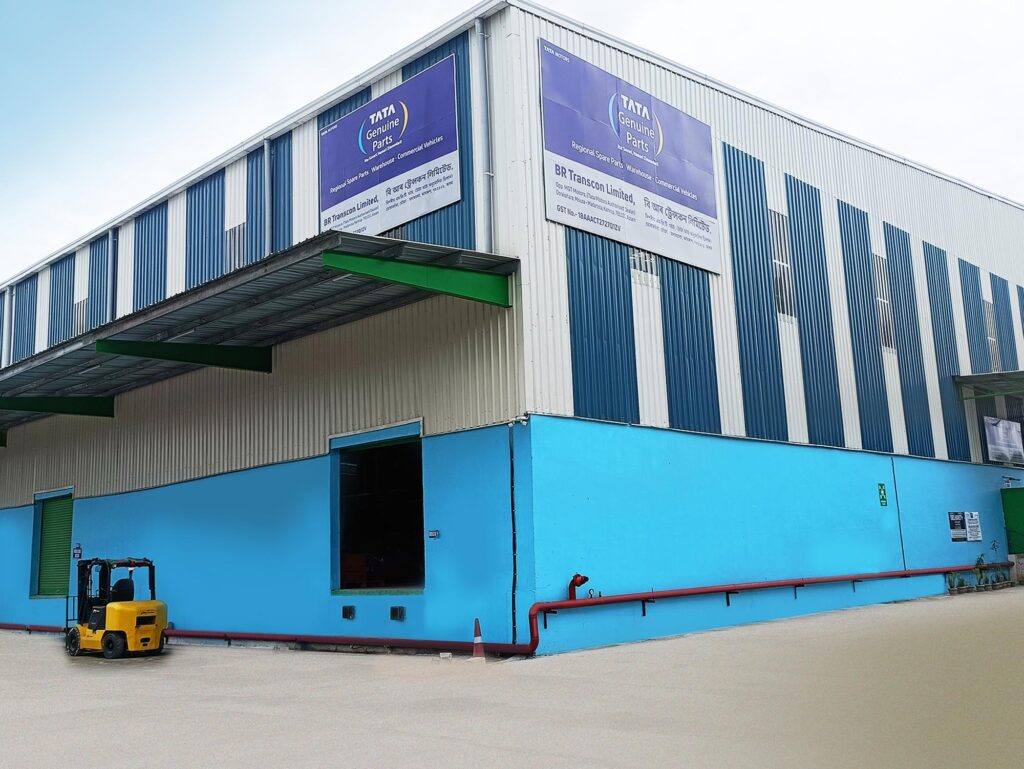
This commitment to excellence extends to our storage practices as well. Specialized care is taken to store spare parts that may potentially have reactions/degradations due to atmospheric conditions. Additionally, a strict First-In-First-Out (FIFO) protocol is maintained, preventing component aging and ensuring customers receive the highest-quality parts.
Do you provide any kind of warehouse management training to your workforce to ensure optimal productivity and efficiency? What are the benefits of Tata Genuine Parts over other parts available in the market?
As part of our improvement journey and continuous learning, our team undergoes regular training on various supply chain processes that include warehouse management. Standard operating procedures guide the operating team and enable them to perform their role with ease.
Tata Genuine Parts cater to the holistic range of Tata Motors’ mobility solutions. The company offers a comprehensive range of parts ensuring high uptime of Tata Motors commercial vehicles. The Tata Genuine Parts are engineered to meet the specific needs of the vehicles, ensuring that they perform to the highest standards. The spare parts undergo rigorous testing, thereby ensuring reliability, durability, and peace of mind for our customers. Tata Motors offers solutions for all the repair and maintenance needs of customers, which include preventive maintenance and regular servicing or replacement of worn-out parts. Tata Genuine Parts deliver the quality and reliability that Tata Motors commercial vehicle owners expect from the brand of repute.